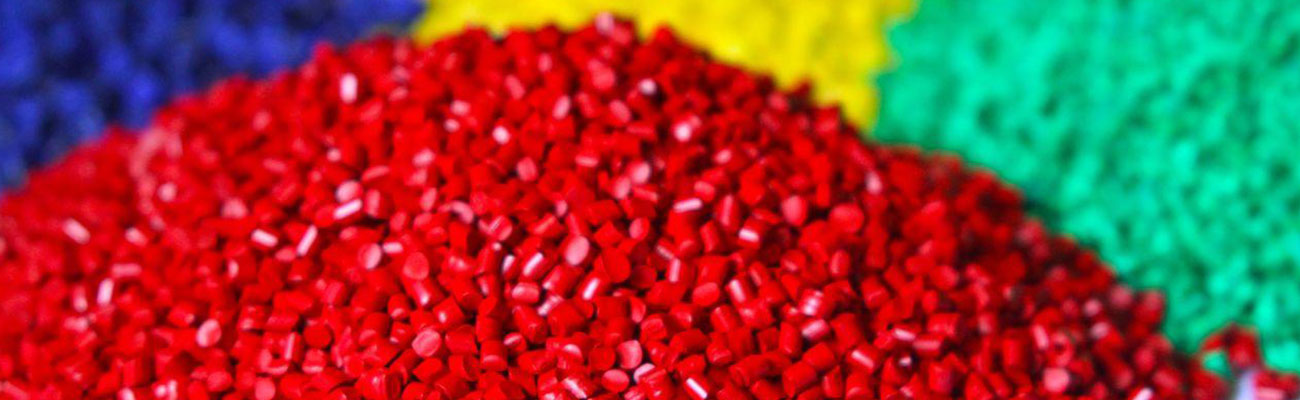
04 May 4 Reasons to Consider Metal to Plastic Conversion
Since the introduction of engineering-grade resins and plastic materials in the 1950s, many parts previously fabricated from metal have been replaced by injection molded parts. On average, companies report an overall cost savings of 25-50% by converting to plastic parts, yet some manufacturers have resisted making the change.
When product manufacturers haven’t considered replacing metal with plastic, it’s likely because they haven’t been informed of the complex qualities that plastic can offer. Others simply appreciate the predictability of using the same material incorporated in the part’s initial design, rather than considering plastic materials that will match or exceed the current material’s performance attributes.
As a production material, plastic blends can be customized to meet specific environmental, structural, and operational demands. The right design and choice of material can produce a plastic component that will outperform metal. Also, adding reinforcing features like ribs and gussets that can be molded directly into the plastic, will improve strength and durability, as well as reduce production time.
When additives are blended directly into plastic, they can bolster specific attributes and create a highly customized material. These additives increase plastic performance in areas such as impact and tensile strength, friction, scratch and flame resistance. Additives make plastics lighter, safer for use in food distribution and medical supplies, and are more environmentally friendly.
Whether you are currently considering making the shift, or uncertainty in the metals market has you looking for viable options, there are plenty of advantages to converting your metal parts to plastic. Here are four considerations to keep in mind:
Better Design
It’s easy to see why engineers love the freedom gained by using plastic injection molded parts over metal counterparts. Design features include:
– When the latest software and technology is used, injection molders can test a variety of materials in the design phase – allowing for predictive design tweaks and stronger performance outcomes
– Ability to integrate and accommodate complex shapes and geometries as well as consolidate parts
– Weight reduction and improved structural limits
– Improved aesthetics – since plastics are available in a wide variety of colors, along with offering surface finishes and textures that are more appealing than metals, plastic injection molded parts tend to dominate metal counterparts. Also, plastic parts allow for enhanced decoration or labeling within the mold, further expanding their aesthetic appeal
Improved Performance
When compared to metal parts, plastic parts are typically up to 50% lighter in weight and offer performance attributes that metals simply can’t beat, including:
– Reduced size, weight, and thickness – when you consider the tight space restrictions when manufacturing small appliances, engines, medical equipment, and technology devices, the fact that injection molded parts can be made to be smaller, thinner and lighter than metal parts, are valuable attributes
– Increased strength and durability – not only can today’s engineered plastics withstand a substantial amount of stress, the plastic parts made from them can hold tight tolerances, making them just as robust and reliable as metal parts
– Resistance to impact, corrosion, and heat – with more than 25,000 engineered plastic materials to choose from, including new blends and hybrid formulations, injection molded parts can be designed to meet very specific performance requirements. Some blends and formulations are ideal for applications that demand impact absorption and need to stand up to corrosive elements and heat resistance
Faster Manufacturing
From a manufacturing standpoint, plastic injection molding offers a faster and more consistent process versus metal parts fabrication – including uniform production, increased customer satisfaction, and decreased warranty claims.
Plastic injection molding also provides the ability to combine multiple components in a single mold design, rather than making several components out of metal and assembling them together. This means that joints that would normally have to be welded can be made seamless in an injection-molded part – usually without a parting line. Additional features include:
– Freedom from maintenance – Unlike metal parts, plastic components do not need coating or painting to protect the material, making them virtually maintenance free
– Longer tooling life – While the tooling cost for a metal part and a plastic part are very similiar, the rate of manufacturing is often slower for metals. Another consideration is that the tooling life for plastic parts is on average ten times that of the life expectancy for a cast aluminum tool
– Easier changes – It’s essentially impossible to switch to a less-expensive metal without going through a complete redesign. However, the cost of resins does not typically affect the mold, which provides a higher level of flexibility with material quality and cost
– Plastic components can be produced more quickly than their metal counterparts by employing cyclical and highly repeatable processes that have fewer overall steps. Unlike metal production processes, plastic part production is often automated, mechanized, and requires minimal supervision
– Plastic injection molds can eliminate the need for secondary assembly processes by producing complex and geometrically variant components in a single step. Post-production metal fabrication often includes welding multiple pieces together, adhering ancillary parts like bearings, and applying protective coatings. Plastic injection molds yield a single, ready-to-use component, accommodating multi-piece designs, integrating supporting pieces, and mixing protective coatings directly into the material.
Reduced Production Time and Cost
Reducing the cost of materials is just the beginning of the savings possible with metal-to-plastic conversion. Many elements contribute to significantly reducing the total manufacturing costs for plastics, including:
-Material market stability – Not only does the price of metals fluctuate in the marketplace, but proposed tariffs and economic uncertainty often translates to higher costs. But the cost of plastics and resins used to manufacture injection molded parts often remains stable
-Energy savings – With lower melt temperatures and the elimination of successive machining steps, injection molding requires less energy than metal part production
-Reduced scrap and waste – The injection molding manufacturing process inherently lessens the scrap and waste that typically accompanies metal fabrication
-Lower shipping and operating costs – Since the size and weight of plastic parts is almost always significantly less than metal counterparts, the costs associated with shipping finished parts to the customer or manufacturer, along with other operating expenses, are reduced. Depending on product type, transportation can even be considered during the component design phase, creating products that nest or stack within each other, optimizing space during transport